Hydraulic dredging is a critical process used in marine, river, and mining applications to remove sediments, debris, and other materials from underwater environments. This method relies on powerful suction and pumping systems to transport dredged materials efficiently, making it essential for maintaining navigable waterways, restoring habitats, and extracting valuable minerals. Unlike mechanical dredging, which relies on buckets and excavators, hydraulic dredging utilizes a continuous flow system, allowing for more efficient sediment removal over large areas.
One of the most crucial factors in ensuring the efficiency and longevity of dredging equipment is material selection. The harsh operating conditions—constant exposure to water, abrasive materials, and corrosive elements—can cause significant wear and tear. Selecting the right materials helps prevent premature equipment failure, reduces maintenance costs, and improves overall dredging performance.
Among the most vital components of any dredging system is the hydraulic dredge pump. These pumps are responsible for moving sediment-laden water through pipelines, making them highly susceptible to abrasion and corrosion. By choosing durable, corrosion-resistant materials, operators can enhance the performance and lifespan of their hydraulic dredge pump while minimizing downtime and repair costs. This blog will explore the key material factors that influence dredging equipment durability and efficiency.
Challenges in Hydraulic Dredging Environments
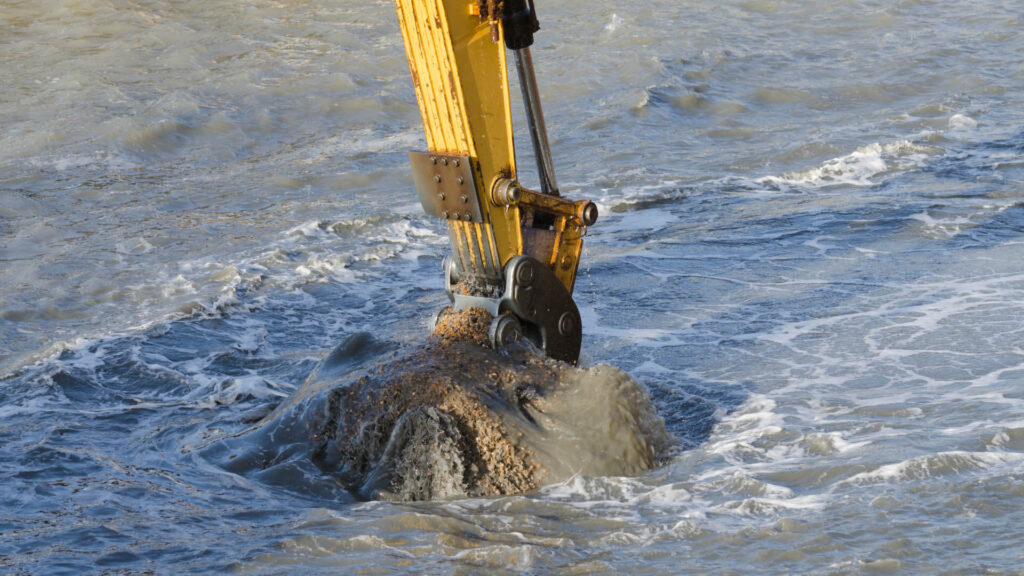
Hydraulic dredging is a demanding process that exposes equipment to some of the harshest environmental conditions. From the corrosive effects of saltwater to the relentless abrasion of sand, gravel, and other sediments, dredging machinery must withstand extreme wear and tear. The success of hydraulic dredging operations depends on the durability of the equipment, and material selection plays a crucial role in mitigating these challenges.
One of the primary concerns in hydraulic dredging is corrosion, particularly in saltwater environments. Saltwater accelerates oxidation and rust formation, leading to structural weakening and premature equipment failure. Components such as the hydraulic dredge pump, pipelines, and cutter heads are especially vulnerable, as they are continuously exposed to water and sediment flow. Without proper material selection and protective coatings, these parts can degrade quickly, resulting in reduced efficiency and increased maintenance costs.
Another significant challenge is the high level of abrasion caused by sediments. Sand, gravel, and other debris constantly pass through the hydraulic dredge pump, pipelines, and impellers, causing gradual material loss. If the pump components are not made from wear-resistant materials, they will experience rapid deterioration, leading to frequent replacements and costly downtime.
Extreme pressures are also a concern, especially in deepwater dredging operations. The hydraulic dredge pump must generate sufficient force to transport sediment through long pipelines, which subjects its internal components to intense mechanical stress. Without materials that can withstand these pressures, cracks, deformations, and system failures can occur.
Common failure points in dredging equipment include worn impellers, eroded pump casings, corroded pipes, and damaged cutter heads. Addressing these issues through strategic material selection ensures greater longevity and reliability, ultimately improving operational efficiency and reducing downtime in dredging projects.
Key Material Properties for Hydraulic Dredging Equipment
Material selection is a crucial factor in ensuring the longevity and efficiency of hydraulic dredging pump. Dredging operations expose machinery to extreme conditions, including corrosion, abrasion, impact forces, and high pressures. To maintain performance and reduce maintenance costs, equipment must be built from materials that can withstand these environmental stresses.
Corrosion Resistance
One of the biggest challenges in dredging operations, particularly in saltwater and chemically aggressive environments, is corrosion. Prolonged exposure to seawater, industrial waste, and other contaminants can cause metals to deteriorate, leading to weakened structural integrity and premature failure. Components such as the hydraulic dredge pump, pipelines, and impellers must be made from corrosion-resistant materials like stainless steel, high-chromium alloys, or coated carbon steel to withstand these harsh conditions. Applying protective coatings such as rubber linings, epoxy coatings, or cathodic protection can further enhance corrosion resistance.
Abrasion Resistance
Dredging often involves transporting highly abrasive materials such as sand, gravel, and slurry. The constant flow of these materials through the hydraulic dredge equipment and pipelines can cause significant wear and tear. Using high-hardness materials like high-chromium white iron, polyurethane, or ultra-high-molecular-weight polyethylene (UHMW-PE) can significantly extend the lifespan of dredge components. Impellers, pump casings, and wear plates must be designed to handle continuous abrasion to avoid frequent replacements and costly downtime.
Impact Resistance
Dredging environments can be unpredictable, with large debris and unexpected obstructions present in the water. Equipment components, especially cutter heads and pump casings, must have high impact resistance to prevent cracks or fractures. Materials like ductile iron, reinforced rubber, and composite materials are commonly used to absorb shocks and protect critical components from damage.
Mechanical Strength
The hydraulic dredge pump operates under extreme pressure, particularly in deepwater dredging applications. The materials used in pump casings, impellers, and structural components must have high mechanical strength to withstand these forces without deformation. High-strength steel alloys and reinforced composites provide the necessary durability for sustained operation. Selecting the right materials ensures that dredging equipment remains efficient and reliable, even under demanding conditions.
Common Materials Used in Hydraulic Dredging Equipment
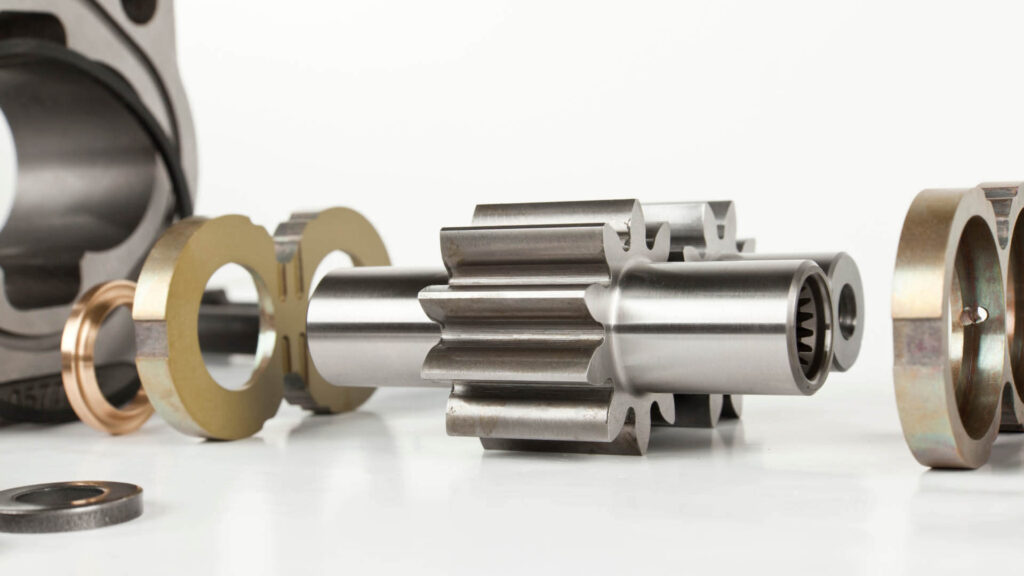
Material selection is one of the most critical factors in ensuring the efficiency, durability, and longevity of dredging equipment. Since hydraulic dredging exposes machinery to extreme conditions, including abrasion, corrosion, and impact forces, the right materials must be chosen to withstand these stresses. The components of a hydraulic dredge pump, pipelines, and cutter heads require different materials depending on their function and the operating environment. Below are the most commonly used metals and non-metallic materials in dredging equipment.
A. Metals
Stainless Steel
Stainless steel is widely used in hydraulic dredge pump components due to its exceptional corrosion resistance. Grades such as 316 stainless steel and duplex stainless steel offer superior resistance to saltwater and chemically aggressive environments. These materials are often used in impellers, casings, and other critical components that come into direct contact with water and sediments. While stainless steel is highly resistant to rust, it is more expensive than other materials, making it a strategic choice for parts requiring long-term durability.
High-Chromium White Iron
For components subjected to extreme abrasion, high-chromium white iron is a preferred material. Dredge equipment impellers wear liners, and other high-wear components benefit from this material’s exceptional hardness and resistance to erosion. However, white iron is relatively brittle compared to other metals, making it less suitable for applications that require impact resistance.
Carbon Steel with Protective Coatings
Carbon steel is commonly used in structural components and pipelines due to its high mechanical strength and affordability. However, since it is prone to corrosion, it must be coated with protective layers such as epoxy, rubber linings, or ceramic coatings to extend its lifespan. This material is often used in large structural parts of dredging systems that require both strength and cost-effectiveness.
Aluminum Alloys
Aluminum alloys provide a lightweight alternative with moderate corrosion resistance. While they are not typically used for submerged components, they are ideal for structural parts, frames, and non-critical dredging equipment where weight reduction is a priority.
B. Non-Metallic Materials
Rubber-Lined Components
Rubber linings offer flexibility and impact resistance, making them ideal for dredge pump liners, discharge hoses, and pipelines. These linings help absorb shocks from large debris and prevent excessive wear caused by abrasive slurry. Additionally, rubber coatings provide some level of corrosion protection, enhancing the longevity of metal components.
Polyurethane and UHMW-PE (Ultra-High-Molecular-Weight Polyethylene)
Polyurethane and UHMW-PE are widely used for their superior wear and impact resistance. These materials are commonly applied in pipe linings, suction inlets, and pump components to minimize damage from sediment-laden water. Their ability to withstand harsh dredging conditions makes them an excellent choice for extending the service life of key equipment.
Ceramic Coatings and Composite Materials
To further enhance durability, ceramic coatings and composite materials are used in high-wear areas of dredging equipment. Impellers, cutter teeth, and hydraulic dredge pump liners benefit from ceramic coatings, which provide additional protection against abrasion. These advanced materials help reduce maintenance costs and improve overall equipment reliability in hydraulic dredging applications.
Corrosion Prevention Strategies for Hydraulic Dredging Equipment

Corrosion is a major challenge in hydraulic dredging, particularly in saltwater environments where metal components are constantly exposed to moisture and aggressive chemical reactions. Without proper preventive measures, corrosion can lead to equipment failure, costly repairs, and operational downtime. Implementing effective corrosion prevention strategies is essential for maintaining the longevity and efficiency of dredging machinery, including the hydraulic dredge pump and pipeline systems.
Protective Coatings
One of the most effective ways to prevent corrosion is through protective coatings. Epoxy coatings, rubber linings, and ceramic coatings provide a barrier between metal surfaces and corrosive elements. Epoxy coatings are widely used on dredge pump casings and pipelines to shield them from saltwater exposure. Rubber linings help protect internal pump components and pipelines from both corrosion and abrasion. Ceramic linings, often applied to impellers and high-wear areas, add an extra layer of protection while increasing durability.
Cathodic Protection
Cathodic protection is a widely used technique to control metal corrosion in submerged dredging equipment. It involves using sacrificial anodes (such as zinc or aluminum) that corrode in place of the equipment, thereby protecting components like the hydraulic dredge pump and hull structures. Another approach is impressed current cathodic protection (ICCP), where an external electrical current is applied to counteract corrosion. This method is particularly effective in saltwater applications.
Regular Maintenance and Flushing
Routine maintenance is crucial in preventing the buildup of corrosive sediments. Regular flushing of dredge pumps, pipelines, and other submerged equipment removes trapped debris and reduces the risk of corrosion. Additionally, inspecting components for early signs of rust or pitting can help operators take corrective action before major failures occur.
Proper Material Pairing
Using compatible metals in dredging equipment helps minimize galvanic corrosion, which occurs when dissimilar metals interact in an electrolyte solution. Selecting the right material combinations for fasteners, pump casings, and impellers can significantly reduce corrosion risks and extend equipment lifespan in hydraulic dredging applications.
Material Selection for Hydraulic Dredge Pumps
Choosing the right materials for hydraulic dredge pump components is essential to ensure long-term performance, durability, and cost-effectiveness. Since these pumps handle abrasive sediments, corrosive water, and extreme pressures, selecting the optimal material for casings, impellers, and wear plates is critical in hydraulic dredging operations.
Comparison of Materials for Hydraulic Dredge Pump Components
- Pump Casings
- High-Chromium White Iron: Offers superior abrasion resistance, making it ideal for dredging applications with high concentrations of sand, gravel, or slurry. However, it is brittle and may not withstand impact forces well.
- Stainless Steel (316, Duplex): Provides excellent corrosion resistance, especially in saltwater environments. While more expensive, it extends equipment lifespan in chemically aggressive dredging conditions.
- Carbon Steel with Protective Coatings: A cost-effective option that requires epoxy or rubber linings to prevent corrosion. Suitable for freshwater dredging operations.
- Impellers
- High-Chromium White Iron: The preferred material for impellers in hydraulic dredging due to its exceptional wear resistance. However, its brittleness may pose issues in environments with large debris.
- Polyurethane-Coated Impellers: Used in certain dredging applications where impact resistance is prioritized over abrasion resistance.
- Stainless Steel: A reliable choice for saltwater environments, offering corrosion resistance with moderate abrasion protection.
- Wear Plates and Liners
- UHMW-PE (Ultra-High-Molecular-Weight Polyethylene): Provides outstanding abrasion resistance and impact absorption. Commonly used in pump liners and discharge areas.
- Ceramic-Coated Plates: Enhance wear resistance, extending the service life of pump interiors.
Trade-offs Between Cost, Durability, and Lifespan
- High-chromium white iron offers excellent durability but is expensive and brittle.
- Stainless steel provides corrosion protection but is costly.
- Carbon steel is affordable but requires regular maintenance.
Recommendations for Different Dredging Environments
- Saltwater dredging: Stainless steel or coated carbon steel for corrosion resistance.
- High-abrasion environments: High-chromium white iron for pump components.
- Freshwater dredging: Carbon steel with protective coatings for cost efficiency.
Selecting the right materials ensures hydraulic dredging pumps operate efficiently, minimizing downtime and maintenance costs.
Conclusion
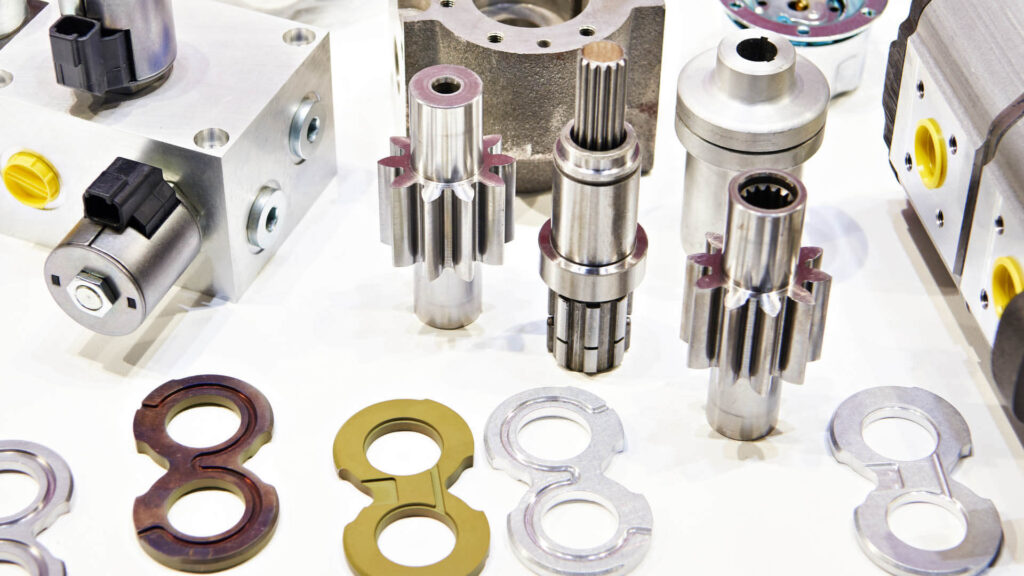
Material selection plays a critical role in ensuring the efficiency, durability, and longevity of equipment used in hydraulic dredging. Given the harsh conditions of dredging operations—ranging from abrasive sediments to corrosive saltwater environments—choosing the right materials can significantly reduce equipment wear, minimize downtime, and extend operational lifespan.
When selecting materials for hydraulic dredge pumps and other components, factors such as corrosion resistance, abrasion resistance, and mechanical strength must be prioritized. Stainless steel and coated carbon steel are ideal for corrosion protection, while high-chromium white iron and UHMW-PE provide superior abrasion resistance in high-wear areas. By investing in the right materials, operators can optimize performance and lower maintenance costs.
To maximize efficiency in hydraulic dredging, it is essential to implement proactive maintenance strategies, including protective coatings, cathodic protection, and regular inspections. Investing in high-quality, durable materials ensures long-term success in hydraulic dredging operations, improving reliability and reducing operational disruptions.